Köster-Group
Defect management in the sharing process
Defect management and interface application
© Köster GmbH, Osnabrück
The Köster Group, with Köster GmbH and its wholly owned subsidiaries Baresel Tunnelbau GmbH and Köster Planung GmbH, is a leader in building construction, civil engineering and tunnelling in Germany. As a standardised solution for the efficient processing of construction defects is essential given the considerable size of the company with more than 1,800 employees, the general contractor took a close look at four software providers in a pilot study in 2013. With mydocma MM for defect management and mydocma SH for automatic data synchronisation with clients, edr software was awarded the contract.
Initial situation
The Köster Group completes around 300 construction projects every year: ARENA 2016 research campus in Stuttgart, Holiday Inn in Düsseldorf, school and administration centre in Dresden, ‘Gazeley’ logistics centre in Mannheim… – the reference list is endless and is characterised by great diversity. Given the wealth of properties, it was obvious that the management team made the decision in 2013 to optimise the defect management processes with software. An isolated solution was out of the question; instead, those responsible were looking for a product that would be able to communicate with other systems through appropriate interface programming. In addition, they only considered an application that would allow them to keep a close eye on all of the Group’s defect processes. For reasons of data security and due to the excellent expertise within their own IT department, their search was aimed at an in-house solution, i.e. deployment was to take place later in the local network.
Before introducing the right software, the market was thoroughly analysed. In line with the principle ‘Trust is good, control is better’, the group of companies launched a one-year pilot phase in which they put four selected software products to the test in two construction projects each under real-life conditions.
Solution
mydocma MM as a purchase version was the solution of choice for Köster: during the trial phase for the construction of the Steigerwald Stadium in Erfurt and the Business Centre II administration building in BraWo Park in Braunschweig, the solution won the race and has been serving the large construction company well since 2014. ‘The company-wide and open approach convinced us,’ summarises Carsten Busse, member of the management board. ‘Thanks to the cross-project evaluation options, we have the right tool at hand to precisely monitor and optimise all processes in defect handling.’ The company appreciates ‘the successful combination of powerful software and a wide range of services’. This is because the pragmatic IT service provider provides advice and support in all important phases of the process chain: from the initial workshop to record existing processes, to the customised configuration of the company solution and on-site training.
Benefits and advantages
mydocma SH – a connecting element in the system landscape
Master data synchronisation via the REST API interface
Two possible application scenarios were discussed for the necessary synchronisation of master data with mydocma MM: Either via the REST API interface or via the universal interface management mydocma SH from edr software, which allows all systems, such as Excel, ERP or CRM solutions, to interact with each other without any problems. Due to the excellent IT expertise within the company, the decision committee at Köster chose the option of connecting mydocma MM to the already implemented RIB business partner, order and project management system via REST API. All relevant information from the operational, technical and commercial areas is brought together in a structured manner in this system. In this way, the company ensures that congruent basic subcontractor data such as company, address, contact person, email, trade, contract and other project variables are transferred from the central database to mydocma MM and synchronised on a daily basis. ‘This is a huge efficiency gain for us, as it keeps the data for defect management up to date without manual intervention and automatically transfers access rights from our project management software,’ enthuses Dany Prescod, project controller at Köster and responsible for continuous improvement processes (CIP) in the company.
Client integration with mydocma SH – an ace up your sleeve for future customer support
In its plans for 2019, Köster intends to utilise the great potential of the flexible interface application mydocma SH even more than before: Instead of granting clients access to the local IT landscape, the general contractor will provide them with their own defect management system in the edr software cloud on request. This allows them to easily link their independent mydocma MM system with those of their clients in order to synchronise relevant data. Having already been successfully tested in three pilot projects, this approach is set to make customer service even more attractive in future.
The automatic transfer of defects and status changes saves both sides valuable time and the standardised spatial structure means that the location is always clear for everyone involved. Everyone remains ‘master’ of their own data, as no one interferes with the other’s system environment. Error-prone and time-consuming duplicate data entries are a thing of the past thanks to the sharing principle: photos, plan sections, defect master data such as the structure tree, trade lists or warranty periods are simply transferred, which increases the quality of the data enormously and saves the project participants bureaucratic work such as defect letters.
Das Hosting und die Betreuung von Kösters externen Anwendern liegt dabei einzig und allein in den Händen der edr software: Sie können dort Serviceleistungen inklusive der Hotline in Anspruch nehmen, so dass für den Bauunternehmer mit mydocma SH ausschließlich ein Nutzen und keinerlei Mehraufwand verbunden ist. Um Berührungsängsten bei den Bauherren entgegenzuwirken, sind ihre Versionen entsprechend einfach konfiguriert und leicht zu handhaben.
edr software – pioneer for mobile defect management
Compared to its competitors, the Munich-based IT service provider started developing a corresponding app at an early stage, which means that mydocma MM mobile offers extremely sophisticated user guidance and thematic depth. ‘Our company benefits greatly from the fact that site managers can record and check defects directly on the construction site in no time at all using a mobile phone or tablet,’ praises project manager Prescod. ‘As the app is very intuitive, our users can get started with mobile defect management without much training.’ Technical conveniences such as photo documentation, voice recognition or location recognition via QR codes ensured a high level of acceptance among employees.
Conclusion
‘With edr software, we have a business partner at our side that impresses us with both its IT expertise and its understanding of construction processes,’ says Managing Director Busse. ‘The user-friendly software products are technically and professionally sound.’ The IT company, which emerged from the engineering company EDR, knows what is important when it comes to the digitalisation of business processes and understands how to generate competitive advantages for its clients in line with the motto ‘Many roads lead to the customer’: The mydocma SH interface application is the icing on the cake, especially for defect management of this magnitude, as it easily connects project participants across company boundaries and enables extremely efficient collaboration. According to the responsible project manager, edr software’s well-organised service package with telephone hotline, e-mail support, 1:1 consulting via Teamviewer, etc., also deserves the highest praise – it ensures a consistently smooth workflow for the mydocma MM users, so that they can concentrate on their actual core tasks at all times.
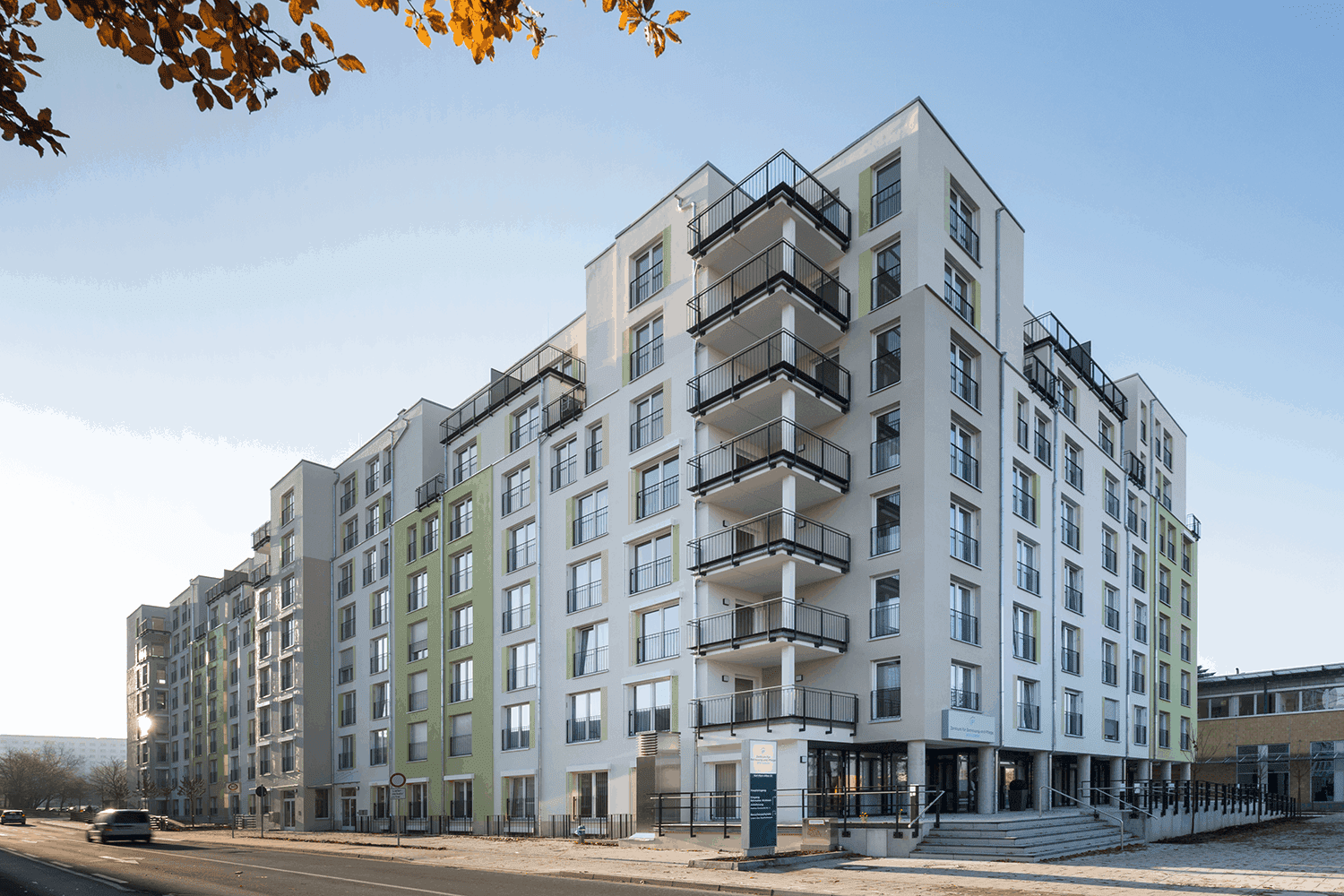
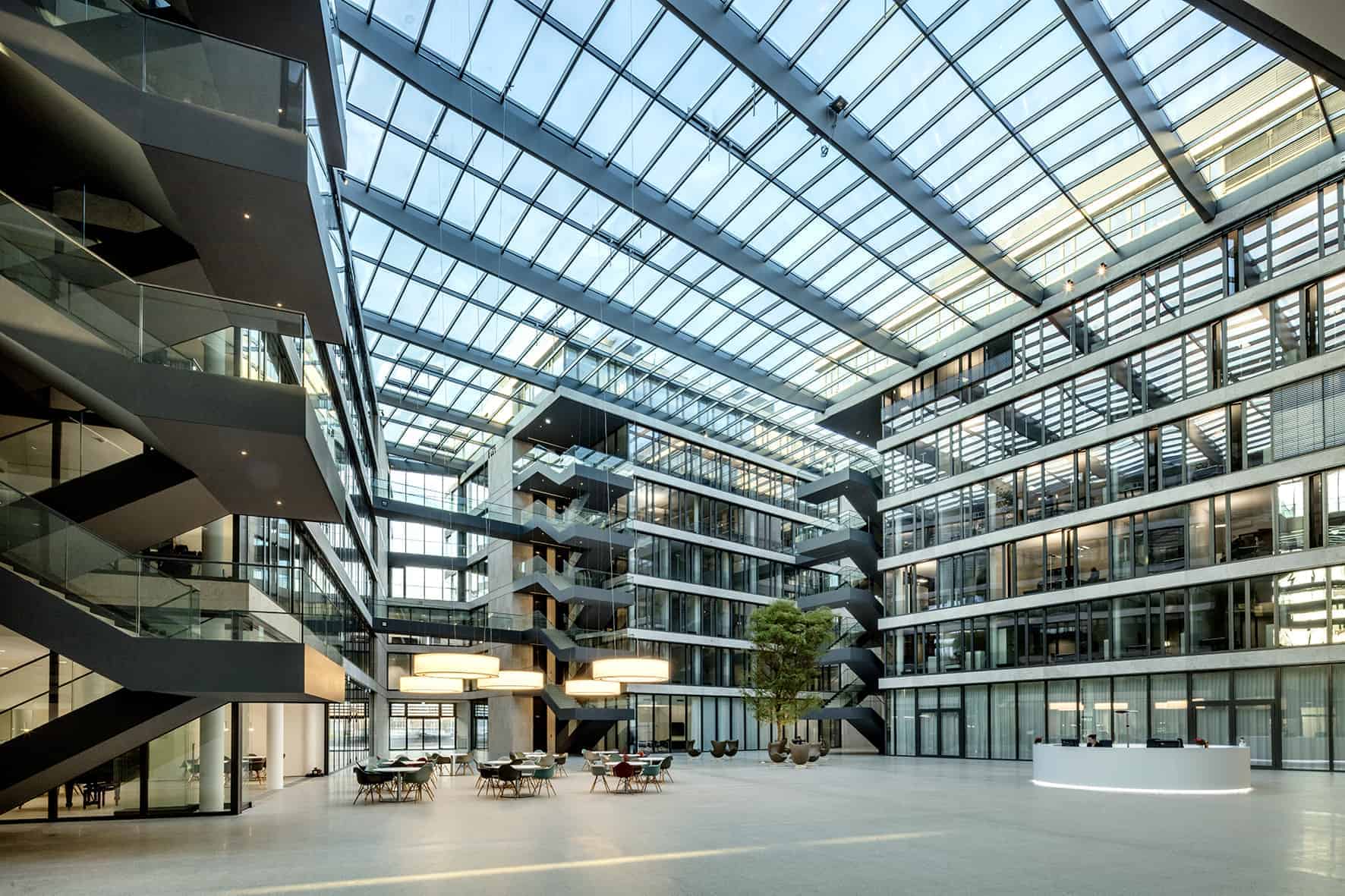
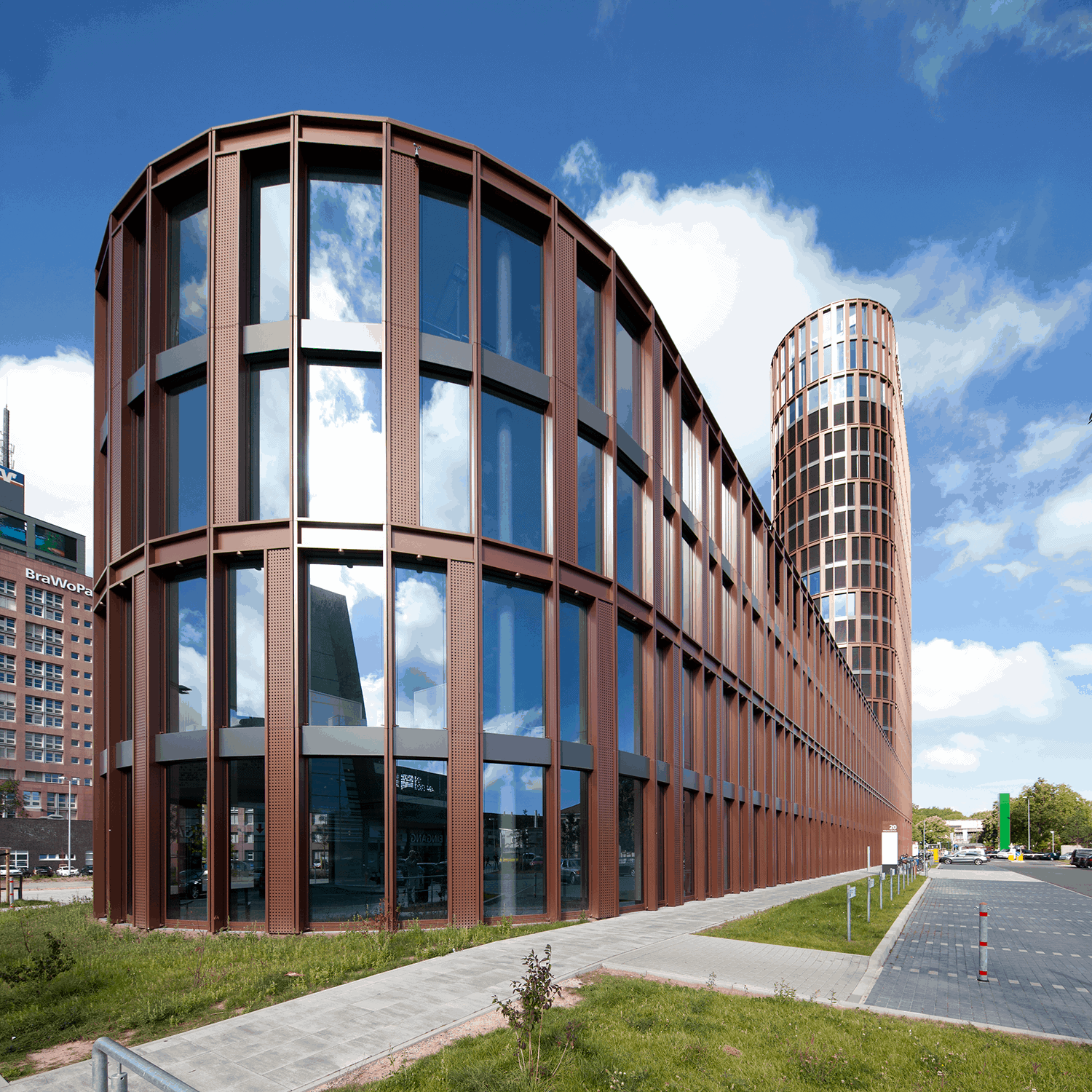